As an extremely important component of your Heavy Equipment’s cooling system, coolant can help prevent cavitation, corrosion, freezing, and rust. A periodic inspection of your Heavy Equipment’s coolant can provide information that is important to performance and health.
Most heavy-duty antifreeze is approximately 95% ethylene glycol and 5% water and additives. Approximately 1% of all antifreeze is manufactured using from propylene glycol, which is less toxic but more expensive than ethylene glycol. When glycol is mixed with water, coolant is created. Most coolant is 30% - 50% glycol. Additives are incorporated to fight corrosion, rust, scale, and they also help to protect wet cylinder sleeves from cavitation.
Choosing the right coolant and periodically inspecting it can work wonders for your cooling system. Follow these recommendations for optimal cooling system health and performance.
Buying Coolant for My Heavy Equipment
• Check to see if the coolant you purchase for your Heavy Equipment states that it complies with ASTM standard D-6210 on the package.
• Deionized water should be used for all Heavy Equipment coolant. Most (if not all) diesel coolants should be prediluted.
• When you find a coolant you are happy with, stick with it. Never mix them. Always follow the maintenance suggestions from the manufacturer.
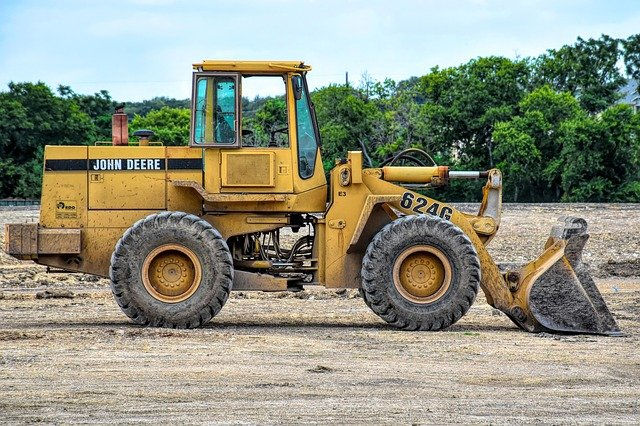
Coolant Maintenance Recommendations
• Periodically conduct visual tests. The coolant should be clean and free of rust coloration.
• Get a heavy equipment coolant analysis test kit. The recommended interval for testing is 1,000 hours.
• Be sure to note the color changes on the test kit strips as they can indicate freeze/boil point (glycol content) and nitrite levels. Some test strips will also indicate PH balance.
For more information on coolant, ask a diesel technician at your next visit to Flying Wrench Services or call us today at: (360) 638-0044.
Comments